It’s encouraging to view MotoGP R&D as important for advancing motorcycle design as warfare accelerates technological progress. In truth, development has always been hostage to regulations, never more so than with today’s dumbing down into cost-saving conformity… not even cylinder bore size is free.
Advances have been confined to minor (if important) aerodynamics and active ride-height adjustment. But 2023 did see something fundamental: KTM’s carbon-fibre chassis – but hardly an innovation. Carbon fibre was first used in the 1980s. It fell out of favour for probably all the wrong reasons – for in racing convention outranks invention. Copy, but improve.
Early non-metallic efforts came from Britain. Notably from the-then independent Suzuki team as the factory had temporarily taken a back seat. Innovative designer Nigel Leaper adapted honeycomb-sandwich into a folded and bonded chassis for the square-four engine. Ridden by Rob McElnea and Niall Mackenzie, the former described the ride as “plush”. Both achieved top-10s against full factory Honda/Yamaha opposition.
Leaper designed an autoclaved full-carbon Mk2 for the new V4 the following year, but the “not-invented-here” syndrome saw Suzuki shelve it. Innovation over.
Mackenzie had experience on another British black-frame, the 250 Armstrong. This used a moulded carbon-fibre spine, filled with foam and baked in an autoclave – standard racing car practice. The Rotax-powered bikes, brainchild of Mike Eatough, also had carbon-fibre swingarms. And they performed well, with the other rider, Donnie McLeod, making the podium. A low-budget independent effort by another British designer, Chris Wheatley, appeared briefly in 1986, ridden by Gary Lingham, but made no waves.
The aim back then was for chassis stiffness – a rigid platform for the suspension. Chassis flex was blamed, not incorrectly, for all sorts of wayward handling.
Convention took over, while chassis design moved on. Maximum stiffness, it turned out, was not ideal. At ever-higher lean angles allowed by tyre and suspension development, too much stiffness encouraged what Wayne Rainey dubbed “chatter-bounce”. He addressed it by dumping the stiff factory chassis for a more flexible Harris version.
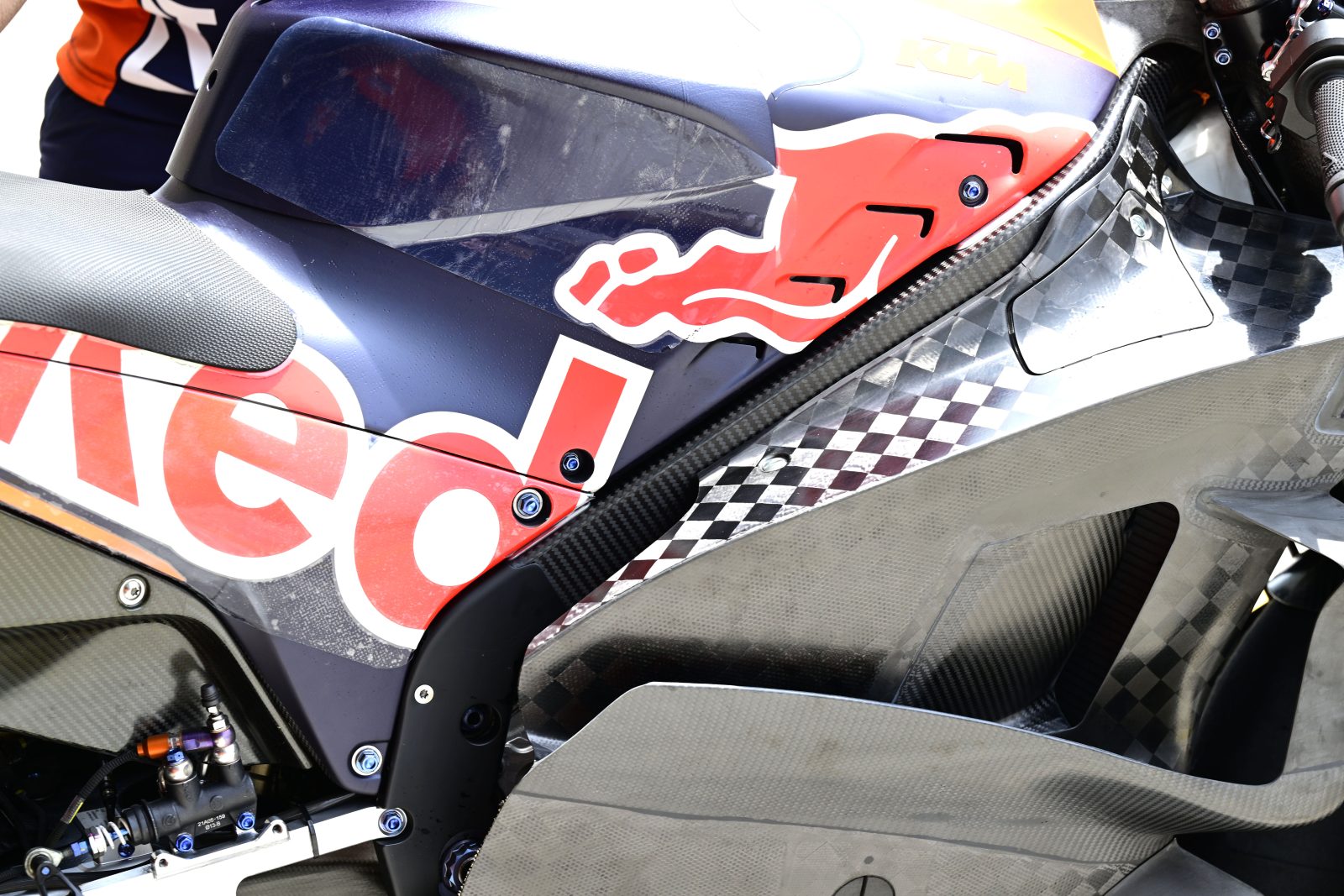
But if maximum stiffness wasn’t right, nor was random flip-flop flexibility. A chassis needed to be rigid fore-and-aft, to absorb braking loads (also increasing) and under power, but to flex laterally, to absorb bumps at full lean, avoiding chatter.
Sounds simple, but it isn’t. The quest for chassis that will bend like a tree (to coin a phrase) remains as absorbing and difficult today as it always was. Much progress has been made, all with aluminium (and for KTM steel-tube) chassis, with carbon thought to be too stiff. But, like money, in racing more is good but is never enough.
There was, however, one believer that carbon fibre, far superior to metal in strength-to-weight, could be made to work. Ducati Corse’s first MotoGP engineer Filippo Preziosi’s innovative style saw him make a minimal carbon-fibre box that combined the function of airbox and main chassis spar. Isn’t carbon too stiff, we asked him? No, he insisted. The material is not important in itself; it is how you use it.
His experiments were not successful, underlined by Valentino Rossi’s failure to continue Casey Stoner’s successes with the Desmo. Preziosi eventually paid the price, replaced in 2013 by current Ducati genius Gigi Dall’Igna, whose prowess has been rewarded with the marque’s current domination.
The first thing Dall’Igna did was to revert to an aluminium chassis. But was Preziosi so wrong?
Stoner recently came to his defence in an interview, saying that it was mainly lack of budget that constrained chassis development. Preziosi was “very clever”, but didn’t have the resources to develop his ideas.
While carbon-fibre swingarms are common, KTM is still the only one to delve into the black arts of carbon chassis construction. Has bike racing finally caught up to F1?
WORDS: MICHAEL SCOTT PHOTOS: GOLD&GOOSE