It only seems a moment ago that manufacturers were thrown into turmoil by the demand to meet stringent Euro 4 emissions laws. That rule-change led to famous models being discontinued and new technologies like ride-by-wire exploding across the market, but it’s already nearing the end of its life. Its replacement – Euro 5 – starts to be phased in on 1 January, 2020.
The new rules actually stem from the same piece of legislation that introduced Euro 4; the snappily-titled Regulation (EU) No 168/2013 on the approval and market surveillance of two- or three-wheel vehicles and quadricycles Passed into law in early 2013, it set out a staged route to reduce bike emissions over a period of years. In January 2016, Euro 4 rules were applied to all newly-homologated motorcycles. In January 2017 the same rules were applied to existing models – although bike firms have managed to use so-called derogation to gain an additional two years of grace to continue to sell small numbers of Euro 3-spec bikes right to the end of 2018.
While the last of those old Euro 3 machines have only recently been withdrawn from sale in the European market, Euro 5 means we can expect another imminent cull and extensive redesigns as current Euro 4-legal models are revamped or replaced to suit the new limits.
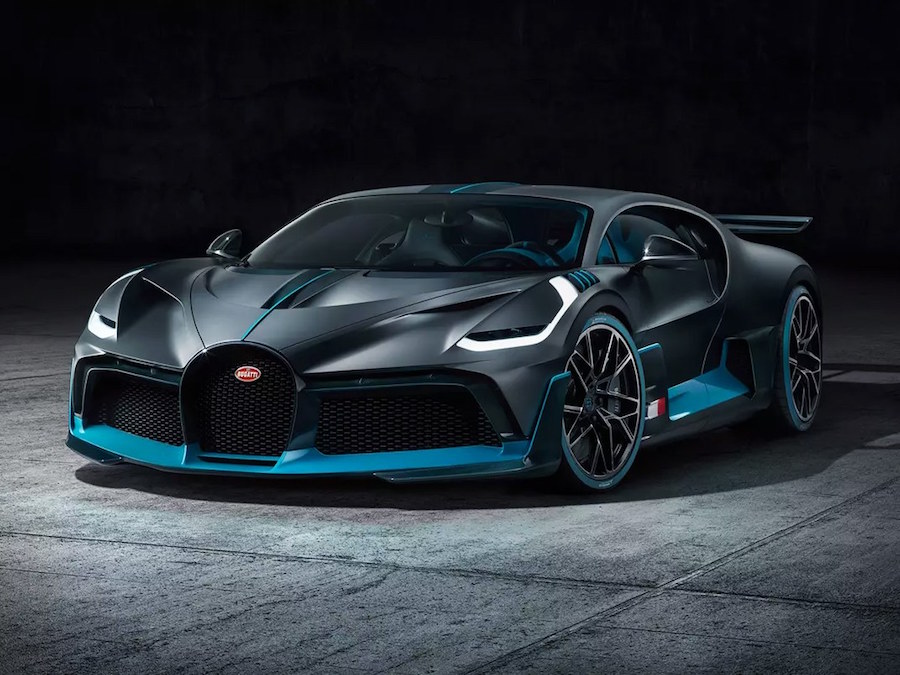
You might think that a piece of European legislation is relevant only on that continent, but European emission rules are fast becoming the closest thing we have to a worldwide standard. Massive international bike markets including India and China also base their legislation on Europe’s emissions limits, and Japan aligned itself with Euro 4 back in 2017.
Even America, which has its own emissions laws and limits, is affected because bike firms design their machines with the EU standards in mind and then modify them, where necessary, to suit the US rules.
Global engineering firm Ricardo might not be a name that’s familiar to all, but in the automotive and motorcycle industries, it’s the company that others turn to when they need engineering help. Confidentiality means Ricardo’s client base is largely secret but projects in recent years include the development of BMW’s K1600 six-cylinder motor and Norton’s new 1200cc V4 superbike engine, while on four wheels you’ll find Ricardo’s fingerprints on supercars from McLaren and Bugatti.
We spoke to Paul Etheridge, head of strategy and business development at Ricardo Motorcycle, and Michael Ryland, who’s the firm’s technical lead on motorcycle emissions, looking after its Euro 5 programmes, to understand how the new rules will affect bikes in 2020 and beyond. As well as being experts in engine design, both men are keen riders; Michael Ryland rides a Triumph Street Triple and Paul Etheridge’s collection includes an original Suzuki Hayabusa, an Indian Chief Vintage, a Yamaha XV1700, a Suzuki GT750A and a Honda CB750K6.
While Euro 5 may be new to most of us, it’s something Ricardo has been working towards for a long time. Paul Etheridge said: “We’ve been living with it for years! It’s quite interesting how different customers have approached it in terms of seriousness and timing. We’ve done several Euro 5 projects for various customers around the world. The first we started in 2013, for a company that was quite forward-thinking and wanted to understand the implications from a very early stage so they could gear up properly for it, while other companies we’re just starting work on it for. Some people lead from the front, some people panic at the last minute…”
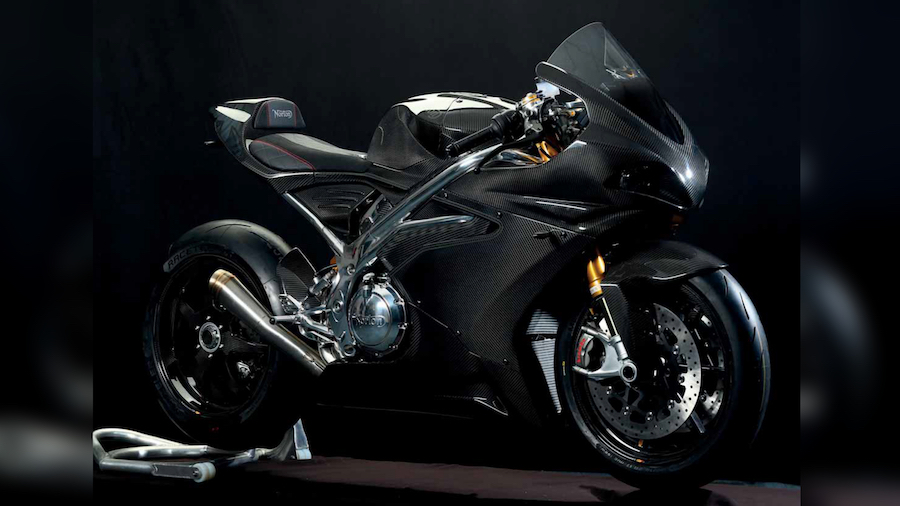
Michael Ryland explained how the Euro 5 standards have changed: “Compared to Euro 4, the emissions limits are much lower, so it’s a considerable challenge for the manufacturers both in terms of meeting the legislation – and particular motorcycles have particular issues with it, some are easier than others – and also meeting it at a reasonable cost.
“The limits have gone down by about a third on average. It’s different for each emissions type. It’s not as big a jump as Euro 3 to Euro 4, however as you decrease these limits it just gets tougher and tougher to meet them as you run out of quick hits for reducing your emissions. So it gets more and more expensive.”
Currently, Euro 4 limits place restrictions on the amount of carbon monoxide (CO), hydrocarbons (HC) and nitrogen oxides (NOx). As well as reducing those totals, Euro 5 adds a limit on the amount of non-methane hydrocarbons in the exhaust, and that’s proving to be a particular challenge for engine designers.
Michael Ryland said: “Hydrocarbons are basically unburnt fuel that’s not been able to fully combust in the chamber, or burn off in the exhaust or catalyst, and non-methane hydrocarbons are simply the ones that aren’t methane. The EU has an assumption that non-methane hydrocarbons make up about 68 percent of your total hydrocarbons. But in reality, on most engines, non-methane hydrocarbons make up more like 90 percent of the total. The real challenge is being able to reduce the emissions for non-methane hydrocarbons without increasing your NOx, because one wants the catalyst to be rich and the other wants the catalyst to be running lean, so you have to balance it very carefully as close as you can to stoichiometric conditions in all transient operation across the test cycle.”
Compared to relatively low-revving cars, bike engines – and high-revving sportsbike engines in particular – have problem when it comes to hydrocarbons. As Michael Ryland explains: “On higher-performance engines you typically have longer valve durations which causes many issues, in particular for the hydrocarbon emissions. It means your exhaust valve is probably opening quite early, which is great for power as it means it’s easier to get the exhaust gasses out, however for emissions it means the combustion process is only partially complete by the time the exhaust valve is opening. That increases the amount of hydrocarbons that are going out of the exhaust by not being burnt. And at the other end, on the valve overlap side [when the inlet valve opens before the exhaust valve closes], you have fuel that’s being injected into the port and it’s just completely skipping the combustion cycle and going straight out of the exhaust port.
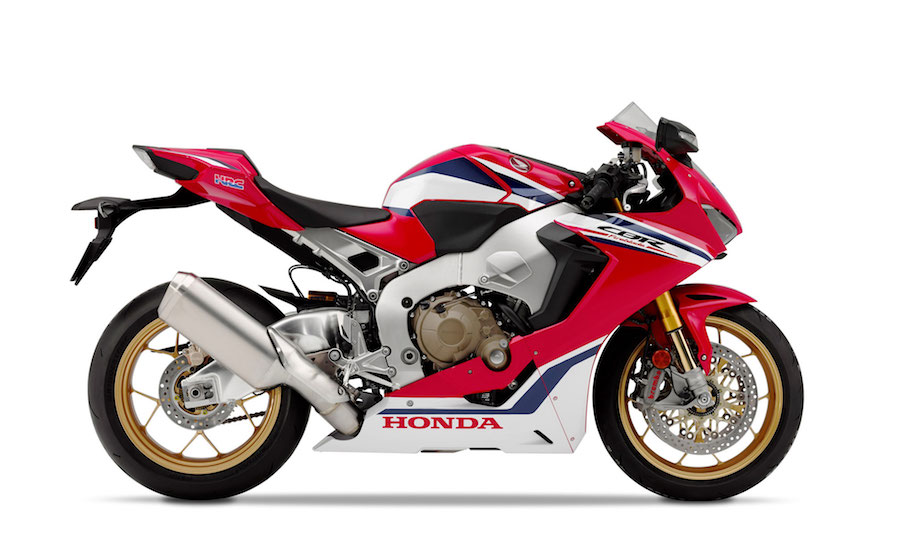
“To reduce those hydrocarbons you do as much as you can with the catalyst, because that’s a nicer solution and when catalysts are warm they get very high conversion efficiency. You can be easily over 95 percent conversion efficiency, which is great. But before they’re warm you’re really struggling.
“Valve overlap also does become a big issue, especially with more aggressive, high-performance engines, so you have to look at strategies for reducing it. That could be additional technology or it could be a lower state of tune for the engine. But because you can’t accept any reduction in power you have to find other means of getting that power back.”
Etheridge said: “Catalysts cost money and the bigger they are and the more precious metal they’ve got in them, the more expensive they are. And also, on motorcycles, the more difficult they are to package. So you want to improve the engine-out emissions as much as possible by improving combustion and optimising valve overlap, things like this, to minimise the emissions that come out of the engine. That also has a benefit in terms of driveability and fuel consumption.”
For high-performance, high-revving bikes, the rules seem perfectly tailored for a push towards variable valve timing technology. It’s already used on machines like the Suzuki GSX-R1000 and several Ducatis, and BMW’s all-new S 1000 RR one-ups them by using variable valve timing and lift.
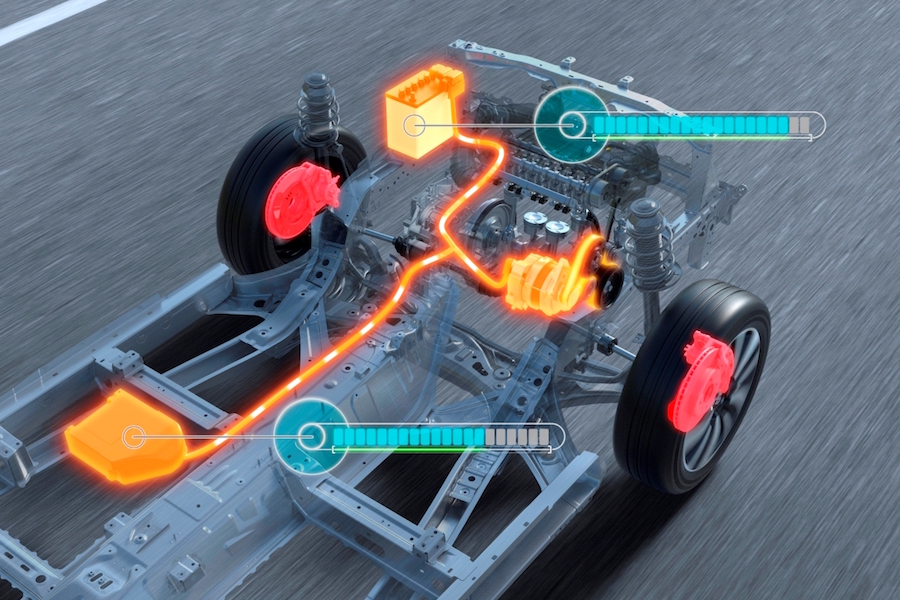
“It’s an enabling technology,” continued Etheridge. “And as with most things, you need something like legislation to get it into the market. Variable valve timing has got a number of benefits, not just enabling emissions compliance but also improving torque curve shape, driveability, combustion stability at light load, and fuel consumption. They’re all positives for the performance of the vehicle. The negatives are, of course, it costs more and you’ve got to package it. But if you think about how motorcycle technology has developed, it’s normally legislation that’s forced the issue and then it becomes commonplace after a while and nobody thinks about it anymore.”
Since variable valve timing and variable valve lift systems are such a panacea you might wonder why it’s taken so long for bikes to adopt them.
“One thing is cost,” explains Etheridge. “And the other thing is that now automotive engines are downsizing the components are more readily available in the right physical size for motorcycles, which perhaps they weren’t in the past. Remember turbochargers on motorcycles in the old days? They were horrendous things, much too big for the engines, they were waste-gated for most of the operating envelope of the engine and very difficult to control. But now turbos are fitted to little 600cc cars in Japan and they’re physically the right size for motorcycles. The motorcycle industry alone never had the volumes that turbocharger suppliers would be interested in gearing up for. It’s economy of scale. Now you can pick up a turbocharger off the shelf that’s the right size and that supplier makes millions of them for cars. The same is true of VVT.”
Ryland points out bikes also need more refinement than cars, saying: “One of the other challenges for VVT or VVL is the fact that motorcycles are much more sensitive to driveability issues. Because the inertia of the powertrain and the whole vehicle is so light, and there’s a huge power-to-weight ratio, any small driveability issues will be felt by the rider very easily. It has to be refined very well.”
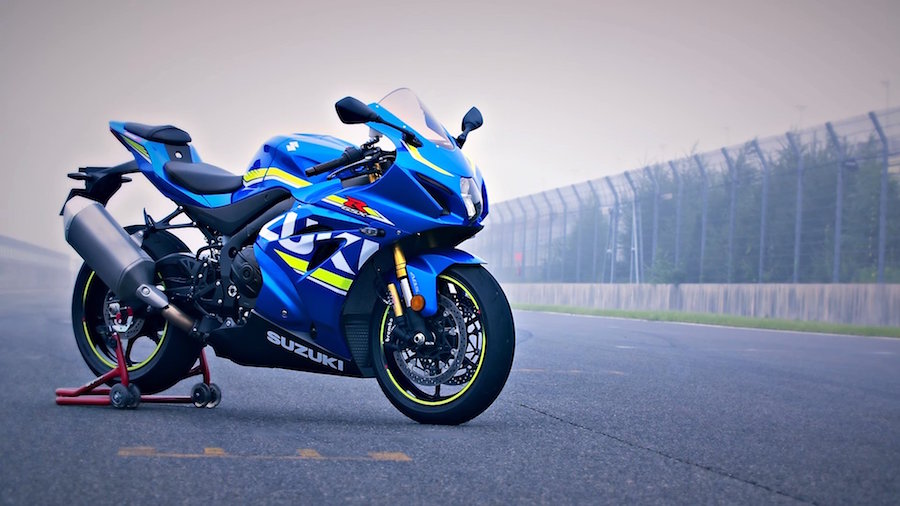
With leading superbikes like Honda’s CBR1000RR and Yamaha’s YZF-R1 nearing the end of their lives, are we likely to see Euro 5 replacements bearing variable valve technology? Etheridge thinks so,: “I think for a situation like that, it’s a no-brainer. For a superbike engine, you’ve got to have it for the future.”
However, he says different types of bikes will use different solutions to achieve Euro 5 limits: “The sort of work we’ve been doing for manufacturers is quite varied. We’ve been working on Euro 5 solutions for bike firms since 2013,” said Etheridge, “We’ve probably done 10 projects of various types, sometimes just looking at their current engine, telling them what they need to do to get it to Euro 5 and letting them go away and do that, and sometimes taking a project all the way through to producing a demonstrator engine with whatever modifications are most appropriate and delivering an engine back to them that has those Euro 5 features on it. We’ve been working on a number of different motorcycle types for a number of different manufacturers, so we’ve got a pretty good handle on what’s needed.
“If you look at the cruiser market, for example, it’s all about look, so they have particular challenges; the exhaust has got to be visible so you can’t just stick a big lump of a catalyst in the way; it might be great for emissions but from a design point of view it’s completely unacceptable. For sportsbikes it’s about maintaining or enhancing performance, while for smaller bikes it’s about minimising the add-on cost. That’s what we’re helping people with today and we’ll be continuing to help them until the legislation is in place.”
Ryland adds: “Each type of engine has its own challenges. High performance engines can’t afford to lose any power, so to achieve an improvement in emissions they’re looking at additional technologies. Whereas low-cost motorcycles have other challenges; they want to remain low-cost, so they can’t afford to add anything that will increase the sale price of the vehicle. That means using the minimum amount of technology possible.
Nine months
New models that go on sale on or after 1 January 2020 will need to comply, however, the bigger hit is likely to emerge 12 months later, with existing models being required to comply from 1 January, 2021.
What about hybrids?
in the car world, there’s been a rapid expansion of using a combination of combustion engines and battery power to achieve better economy, emission and performance. But at the moment there’s little interest in the same technology from bike firms because they can achieve Euro5 limits without resorting to hybrid technology.
“You’re going to need to have an electric motor and a combustion engine, and package it all in a suitable way so you don’t lose the fundamental advantages of the vehicle you’re developing,” says Etheridge. “What’s the point?”
When it comes to pure electric bikes, he says that’s different.
“It’s clear now that people are picking up on this and starting to work on it seriously,” he continues. “What’s not clear is what the most suitable technology is for different sectors of the motorcycle market. For inner-city, small, commuter-type vehicles, it’s a bit of a no-brainer. But for bigger, more premium leisure products, no one has got a clear answer yet as to which way they should be heading in terms of technology development.”
OBD Stage II headaches
When the EU rubber-stamped plans for Euro 5 back in 2013, a key requirement was the addition of on-board diagnostics (OBD) Stage II monitoring systems.
OBD have been a key element of emissions controls in cars for more than two decades, but while current Euro 4 emissions rules demand a basic OBD system which simply alerts you if an emissions-related sensor fails, the OBD Stage II setup planned as part of Euro 5 is proving to be a real headache – so much so that its implementation has been pushed back and remains under discussion at legislative level today.
“Stage I monitors to see if the sensor is broken, Stage II looks at the voltage from sensors to see if they’re giving a reasonable value, and on top of that you have to monitor a lot of the other emissions-critical items such as catalyst monitoring and oxygen sensor monitoring as well as engine misfire-detection,” explains Ryland. “It’s a lot more advanced than OBD I, and a big step up for motorcycles, falling more in line with automotive.”
But why is a system that’s been around for so long on cars proving to be hard to implement on two wheels?
And Etheridge says it’s not as simple as carrying across technologies developed for automotive to motorcycles.
“It’s more complicated than that. If you take misfire detection as an example, an automotive engine might rev to 6000rpm or 7000rpm, but it’s different when you’re trying to monitor misfire on an engine that’s revving to 15,000rpm. So although the existing technologies may be appropriate, the application and calibration of those technologies is a lot more complex and difficult. A motorcycle engine is relatively low-inertia, and you get a lot of feedback from things like bumps in the road, which feedback into the engine through the driveline and can be detected as a misfire even though they aren’t”.
Words Ben Purvis Photography AMCN Archives